Prepreg autoclave process Tool and mould making
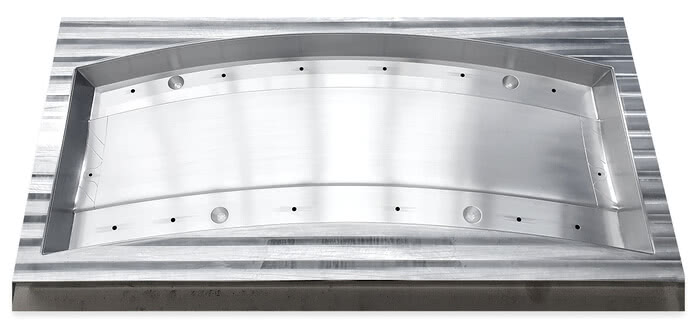
The CFRP manufacturing process "Prepreg Autoclave" is an advanced method for the production of high-performance fibre composite components. This technology enables the precise reproduction of components with optimum force transmission and high surface quality.
Laro NC-Technik's tool and mould making department mills the special moulding tools for the prepreg autoclave process from materials such as aluminium or CFRP, which can withstand the high pressure and temperature requirements of the curing process. Moulding tools can be designed as negative or positive moulds, whereby the side of the component facing the tool achieves a high surface quality and dimensional accuracy.
Laro NC-Technik's tool and mould making department mills the special moulding tools for the prepreg autoclave process from materials such as aluminium or CFRP, which can withstand the high pressure and temperature requirements of the curing process. Moulding tools can be designed as negative or positive moulds, whereby the side of the component facing the tool achieves a high surface quality and dimensional accuracy.
CNC contract manufacturing for the Prepreg autoclave CFRP manufacturing process
The autoclave prepreg process offers outstanding laminate quality and is used in almost all industries due to its numerous advantages. This process can be used to produce components with outstanding optical, mechanical and thermal properties.
CARBON MOULD MAKING FOR THE AUTOCLAVE PROCESSCFRP components of outstanding quality
Laro NC-Technik manufactures the special moulds with excellent surface quality into which the prepreg layers are inserted for the production of your fibre composite components. Depending on your requirements, these moulds are made of materials that can withstand the high pressure and temperature requirements of the curing process. Aluminium or CFRP are frequently used, from which we manufacture one-piece or multi-piece autoclave tools using CNC milling.
Category | Details |
---|---|
Materials | Aluminium, Steel/Stainless Steel, Titanium, Invar, CFRP, GFRP, Plastics |
Part Size | up to 6000 mm |
Part Weight | up to 20 t |
Certification | EN 9100:2018 |
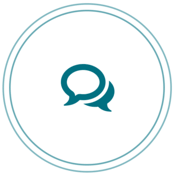
✔ Consultancy
We passionately contribute our wide-ranging repertoire of skills, experience and know-how to your project.
We passionately contribute our wide-ranging repertoire of skills, experience and know-how to your project.
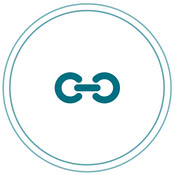
✔ Process chain
Reliable manufacturing through virtualisation, air-conditioned manufacturing and integrated measurement in the machine.
Reliable manufacturing through virtualisation, air-conditioned manufacturing and integrated measurement in the machine.
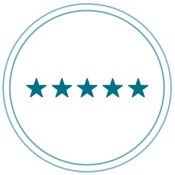
✔ Quality management
We supplement strict certification requirements with regard to quality, reliability and traceability with our personal ambition and commitment.
We supplement strict certification requirements with regard to quality, reliability and traceability with our personal ambition and commitment.
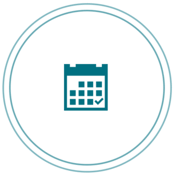
✔ Express milling
Modern machines and short decision-making paths enable express CNC manufacturing for your urgent requirements.
Modern machines and short decision-making paths enable express CNC manufacturing for your urgent requirements.
Prepreg pressing tool production - enquire now and get advice without obligation!
- Moulding tools for simple or highly complex components
- Realise small and large parts at low cost
- Personalised advice and all-round service
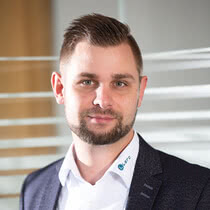
FROM THE ORTHOSIS TO THE HELICOPTER ROTOR BLADECFRP components for extreme requirements
The prepreg autoclave process is regularly used to produce carbon components that have to fulfil special requirements due to the complex and expensive production process. Carbon composites are used in many different industries. Laro NC-Technik has an exceptional range of CNC machines: we are able to mill carbon moulds for delicate components as well as for a carbon rotor blade that is almost 6 metres long.
Aerospace

There is hardly any other field where the demands placed on the parts used are as high as in the aerospace industry. In addition to technical and economic aspects, safety also plays an important role here. Components have to withstand extreme acceleration, mechanical stress and high pressure and temperature differences. And not just temporarily, but over the entire service life of the flying object.
As a DIN EN 9100-certified company, we are very familiar with these requirements. Our many years of experience in this area also flow into the corresponding tools for autoclaves. Prepregging can be used to press components that are perfectly adapted to the conditions in the aerospace industry. We supply the right tools to realise this.
As a DIN EN 9100-certified company, we are very familiar with these requirements. Our many years of experience in this area also flow into the corresponding tools for autoclaves. Prepregging can be used to press components that are perfectly adapted to the conditions in the aerospace industry. We supply the right tools to realise this.
Automotive & motorsport
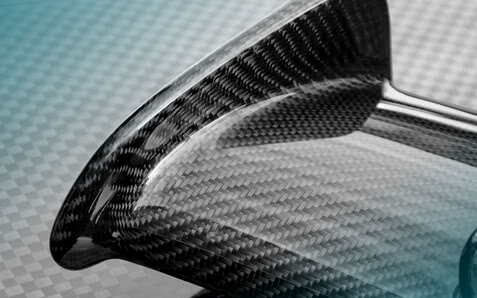
In motorsport with all its facets, man and machine regularly push the limits of what is possible. The individual components of racing vehicles are constantly exposed to extreme loads. Every single component must function absolutely reliably - not least to ensure the safety of the drivers. Components "off the shelf" are often not up to these demands.
The properties of parts laminated using an autoclave, on the other hand, can be precisely influenced. This means that components can also be moulded for motorsport that are adapted to the requirements prevailing there. With our precision-milled moulds for the prepreg autoclave process, we support you in the production of high-quality components. We use modern manufacturing processes to realise your individual requirements economically and quickly.
The properties of parts laminated using an autoclave, on the other hand, can be precisely influenced. This means that components can also be moulded for motorsport that are adapted to the requirements prevailing there. With our precision-milled moulds for the prepreg autoclave process, we support you in the production of high-quality components. We use modern manufacturing processes to realise your individual requirements economically and quickly.
Industry & robotics
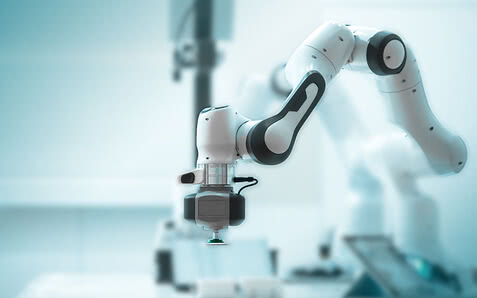
The demands placed on the materials used in the industrial and robotics sectors are constantly increasing. High-quality and lightweight components reduce energy consumption, lower manufacturing costs and increase the performance of the end products. Components from mass production often do not fulfil these requirements. Prepreg lamination processes, on the other hand, can be used to produce optimised parts for every requirement.
Our high-quality autoclave moulds make this manufacturing process safer, simpler and more profitable. The highest quality and the economical, rapid production of your moulds are our performance promise.
Our high-quality autoclave moulds make this manufacturing process safer, simpler and more profitable. The highest quality and the economical, rapid production of your moulds are our performance promise.
Medicine
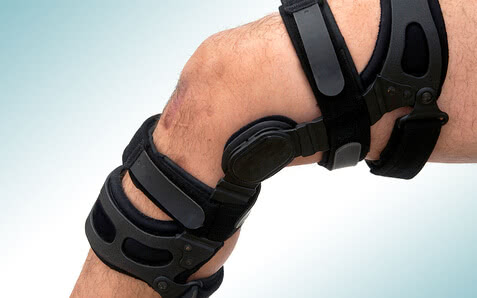
Autoclaves have played an important role in medicine for many years, albeit primarily for the disinfection of medical instruments, for example. However, the prepreg autoclave process is indispensable in orthopaedic technology in particular. Prepreg lamination plays an important role in the manufacture of both prostheses and orthoses (= splints).
Prostheses and orthoses enable people to move in ways that would otherwise be difficult or impossible. The components are exposed to constant stresses and must withstand these safely and reliably over their entire service life. The prepreg autoclave process can be used to mould components that meet these requirements. We manufacture the corresponding moulds exactly according to your specifications and always on time.
Prostheses and orthoses enable people to move in ways that would otherwise be difficult or impossible. The components are exposed to constant stresses and must withstand these safely and reliably over their entire service life. The prepreg autoclave process can be used to mould components that meet these requirements. We manufacture the corresponding moulds exactly according to your specifications and always on time.
Sailing yachts
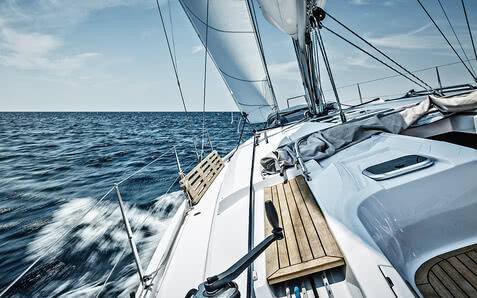
Sailing yachts are sports boats that have a living space and are usually longer than 10 metres. In this area, high demands are placed on the materials used. These include high strength, the lowest possible weight and a visually and haptically sophisticated design. Flagpoles, hatches, covers, panelling and sunroofs in particular are therefore often made from components that have been laminated in an autoclave.
In order to meet the high demands of sailing yacht construction, we offer you high-precision moulds for the prepreg autoclave process. The high degree of automation of our CNC machines enables us to produce autoclave moulds particularly economically. You benefit from a strong price-performance ratio and rapid responsiveness in the event of change requests.
In order to meet the high demands of sailing yacht construction, we offer you high-precision moulds for the prepreg autoclave process. The high degree of automation of our CNC machines enables us to produce autoclave moulds particularly economically. You benefit from a strong price-performance ratio and rapid responsiveness in the event of change requests.
Sports equipment
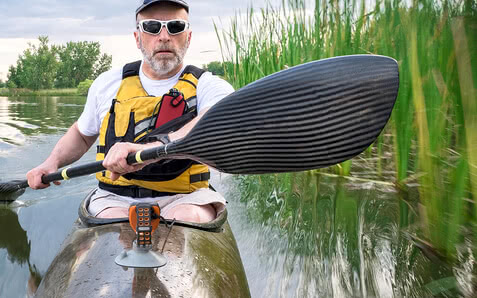
Components manufactured using prepreg lamination are used in a wide variety of modern sports equipment. The high stability and strength, combined with low weight, make prepreg-laminated components the ideal choice for this area of application.
We support you with our high-quality autoclave moulds in the production of durable, high-quality sports equipment parts.
We support you with our high-quality autoclave moulds in the production of durable, high-quality sports equipment parts.
The CFRP manufacturing process Prepreg Autoclave
In the prepreg autoclave process, fibre matrix materials (prepregs) pre-impregnated with resin are cured in a pressure vessel (autoclave) under heat and pressure. The prepregs are cut to size and placed in milled moulds in a specific sequence and orientation. The prepreg layer structure then hardens in the autoclave and can be further processed after cooling. The pressure in the autoclave process and the vacuum ensure that the fibre material is compact and no air bubbles are formed.
Negative and positive moulds for CFRP components
Prepreg autoclave moulds can be designed as negative or positive moulds. The side of the component facing the mould achieves a high surface quality and dimensional accuracy, while the opposite side is formed by the film bag and does not have a defined surface finish. If required, closed prepreg moulds are used: direct contact on both sides with the one-piece or multi-piece autoclave mould gives both sides the desired - smooth or mould-defined - surface finish.
Commissioning and pre-treatment of the carbon moulds
The moulding tools must be pre-treated before use. New moulds are treated several times with a sealer to seal micropores and even out unevenness. This prevents resin from sticking in the prepreg autoclave manufacturing process and improves the surface quality of the component.
After treatment with sealer, release agent is applied to ensure that the finished components can be easily removed from the mould after the curing process. This prevents damage to the mould and component surface due to excessive adhesion.
After treatment with sealer, release agent is applied to ensure that the finished components can be easily removed from the mould after the curing process. This prevents damage to the mould and component surface due to excessive adhesion.
Placing the carbon prepreg layers in the mould
The prepreg autoclave manufacturing process for carbon components begins with the preparation of the prepreg blanks. Depending on the area of application, the appropriate semi-finished fibre products are selected to ensure the required component properties. The cut prepregs are inserted into the mould layer by layer, whereby the defined layer structure is strictly adhered to. This specifies how the individual mats are positioned and aligned in the mould and where reinforcements or other component parts must be inserted.
Vacuuming the mould structure in the autoclave
To ensure a high-quality component surface, the mould is often vacuumed in an "autoclave" for the first time after the first layer has been inserted. An autoclave for prepreg is a device that is used for industrial, scientific and medical processes where increased temperatures and pressures are required compared to the ambient pressure and/or ambient temperature. It allows the targeted setting of negative pressure (vacuum) or positive pressure at the desired temperatures.
Depending on the number of layers, this process is repeated several times in the autoclave process to ensure that the individual layers sit perfectly in the mould contour before the curing process.
Depending on the number of layers, this process is repeated several times in the autoclave process to ensure that the individual layers sit perfectly in the mould contour before the curing process.
Curing in the autoclave under pressure and heat
Once the lamination process is complete, the component including the prepreg mould is vacuum-sealed. A resilient film bag is pulled over the mould and the exposed prepreg surfaces are covered with release film to prevent the absorbent fleece from sticking. The bag is then closed and the air inside is extracted via a valve.
Under the influence of temperature, the previously viscous resin becomes flowable and then hardens, whereby the individual carbon fibre layers are joined to form a CFRP component. The process parameters must be selected according to the requirements of the component and the properties of the prepreg material.
Under the influence of temperature, the previously viscous resin becomes flowable and then hardens, whereby the individual carbon fibre layers are joined to form a CFRP component. The process parameters must be selected according to the requirements of the component and the properties of the prepreg material.
Advantages of carbon composites manufactured using the autoclave process
The different orientation of the superimposed carbon fibres gives the carbon components the desired strength and rigidity. The cured plastic matrix ensures that the fibres are held together in the finished CFRP component, resulting in optimum force transmission between the carbon fibres. This ensures consistently high material quality and outstanding technical properties. The prepreg autoclave technology is characterised by several advantages: perfectly definable fibre placement, ideal carbon fibre content, low porosity, high surface quality and high temperature resistance.
CARBON MOULD CONSTRUCTION IN TOP FORMOur customer service for you right from the start
In CNC service, we are your full-service provider for sophisticated mould construction: carbon components are expensive to manufacture, which is why the quality of the moulding tool plays a decisive role. Our range of services goes far beyond machining. From the initial idea to the finished carbon component, we are the right partner for every project and every stage of the process.
You will be impressed by our customer-orientated company approach: fast response times, adherence to deadlines and openness to new ideas are just a few examples of what makes us stand out as a partner in machining.
You will be impressed by our customer-orientated company approach: fast response times, adherence to deadlines and openness to new ideas are just a few examples of what makes us stand out as a partner in machining.
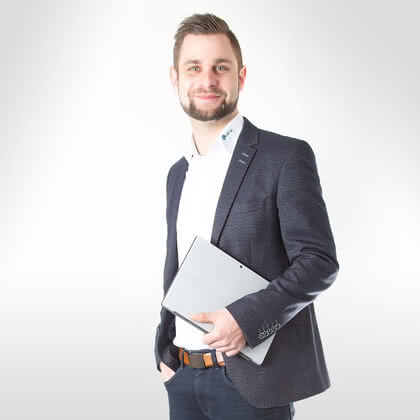
Have we piqued your interest?
Make an appointment now for a non-binding consultation!
Sales
Tobias Kreft
+49 7558 930-514
Send e-mail
VCard downloaden (.vcf)
Make an appointment now for a non-binding consultation!
Sales
Tobias Kreft
+49 7558 930-514
Send e-mail
VCard downloaden (.vcf)